開発プロセス
1:ユーザーとの打合せ
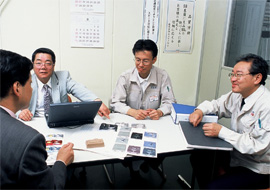
製品の企画段階より金属プレス加工の面から参画し、メーカーの技術担当者やデザイナーとの綿密な情報交換・ディスカッションなど、打合せを行います。様々な製品に携わった経験・技術を基に製品化に向けたご提案をいたします。
2:CAD/CAMシステムで金型を設計
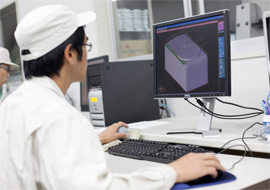
ユーザーとの打合せでえた情報を元に、独自の開発によるCAD/CAMシステムで金型の設計を行います。熟練の技や経験をふまえ、ミクロン単位まで微細に設計することで品質の高い金型をつくることが可能です。
3:NCマシンで金型を加工
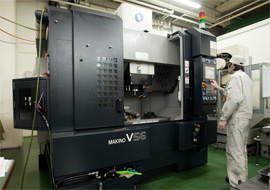
CAD/CAMシステムの情報をNC工作マシンにインプット。コンピュータ制御による高精度の金型を社内工場で瞬時に作成します。小ロット製品にも対応可能です。
4:三次元測定器で検査後、組み上げ
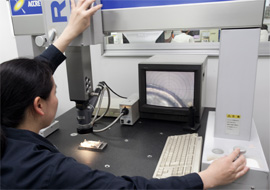
0.5ミクロンの測定精度を誇るカールツァイス社製PMC-850、ミツトヨ製A-12Eで完成した金型を検査。技術者の手で金型を組みたて、微調整を行います。金型のメンテナンス作業もすべて自社で行っています。
5:試作プレスラインでテストを繰り返す
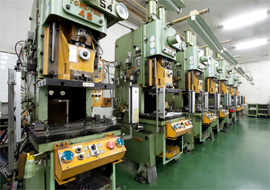
ロゴマークや製品名の浮き彫りダイヤカット加工など、高精度が要求される技術を製造ラインへ乗せるためのテストが何度も繰り返し行われます。
6:自動化された製造ライン
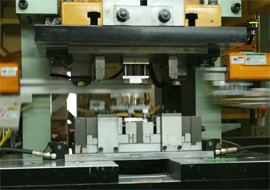
生産ラインは業界に先駆けロボット化を行いました。少量多品種加工にもすばやく対応できる生産システムを構築。生産そのものを集中的に管理できる制御システムも研究しています。
7:製造と同時に自動品質検査
生産ラインは各工程ごとに自動検査機能が働いており、製造と同時に自動品質検査を行います。
また、品質保証の自主認定など、より厳しく品質を検査する機構も設けています。